Understanding the Importance of Injection Mold Tool in Metal Fabrication
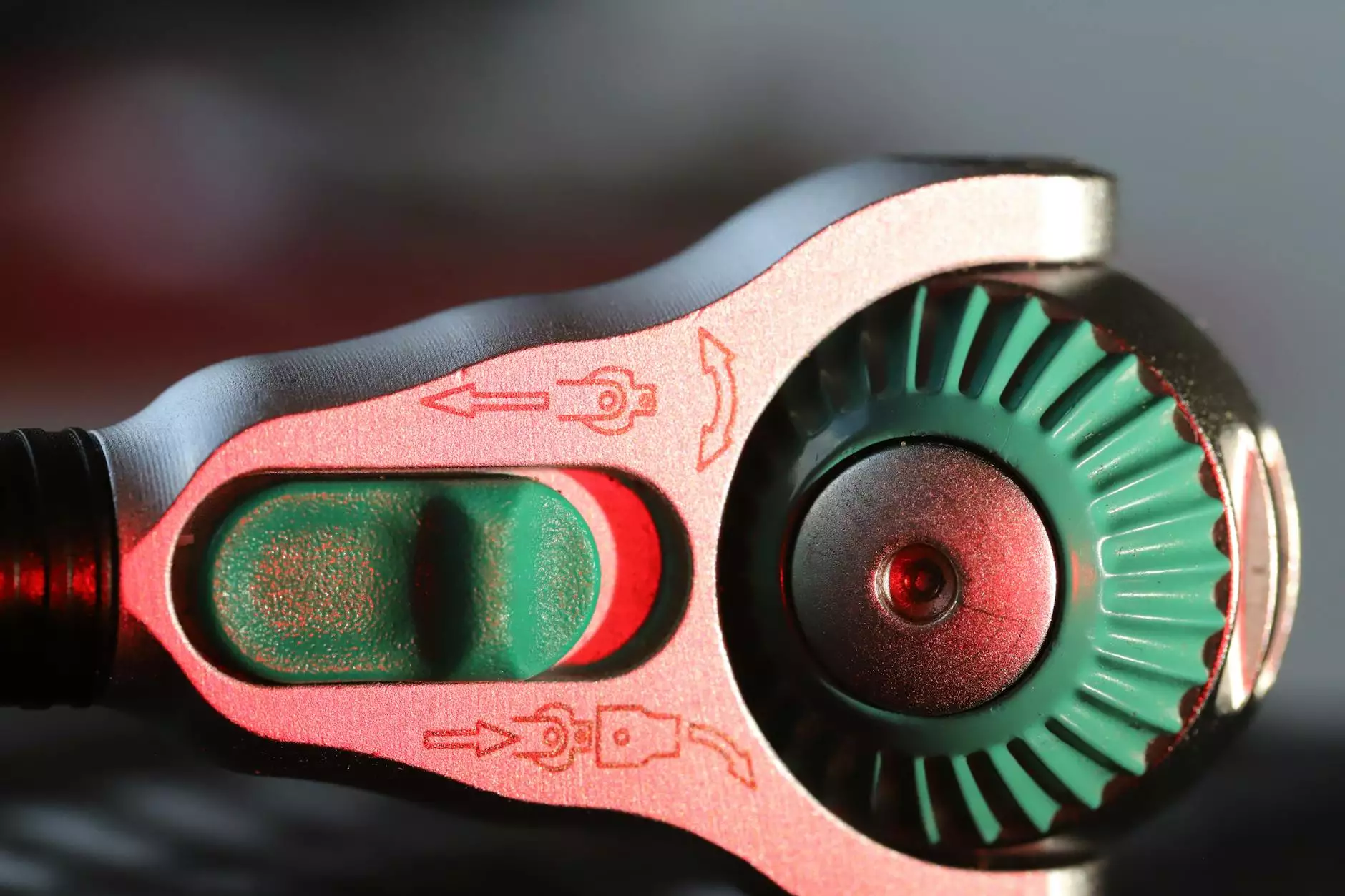
The world of manufacturing is a complex and dynamic environment where efficiency, precision, and innovation are crucial. One of the critical components in this realm is the injection mold tool. This essential tool not only enhances productivity but also ensures high-quality output in various industrial applications. Below, we explore the multifaceted benefits and applications of injection mold tools, particularly in the context of metal fabrication.
What is an Injection Mold Tool?
An injection mold tool is a device used to create parts by injecting material into a mold cavity. Typically, this process involves the use of thermoplastics or thermosetting polymers, but it can also be adapted for metals, especially in specialized applications. These tools are designed to produce high volumes of identical parts with great accuracy and repeatability.
The Injection Molding Process
The injection molding process involves several stages:
- Material Preparation: The raw material is prepared and fed into the injection molding machine.
- Melting: The material is heated and melted to achieve a viscous consistency suitable for molding.
- Injection: The molten material is injected into the mold at high pressure.
- Cooling: The injected material is allowed to cool and solidify within the mold.
- Demolding: The finished part is ejected from the mold, completing the cycle.
Key Benefits of Using Injection Mold Tools in Metal Fabrication
The integration of injection mold tools in metal fabrication offers numerous advantages:
1. High Precision and Consistency
Injection molding provides exceptional precision, which is critical in applications requiring tight tolerances. Consistency in part dimensions ensures that each component fits perfectly, reducing the risk of assembly issues.
2. Enhanced Production Speed
With the ability to produce thousands of parts per hour, injection molding significantly enhances production speed. This rapid throughput leads to higher efficiency and lowers manufacturing costs over time.
3. Versatility in Design
The design flexibility offered by injection mold tools allows manufacturers to create complex geometries that may be difficult or impossible to achieve with traditional manufacturing methods. Consequently, this versatility leads to innovative product designs.
4. Reduced Material Waste
Unlike subtractive manufacturing processes, injection molding minimizes material waste by utilizing the exact amount of material needed for each part. This environmentally friendly approach aligns with contemporary sustainability goals in manufacturing.
5. Scalability
Once the investment in a high-quality injection mold tool is made, scaling up production is seamless. This feature is especially valuable for businesses experiencing fluctuating demands.
Applications of Injection Mold Tools in Metal Fabrication
Injection molds are employed across various sectors, underscoring their universal applicability:
- Aerospace Components: Due to their stringent quality requirements, injection molding plays a vital role in producing aerospace parts with high precision.
- Automotive Industry: From dashboard components to intricate engine parts, the automotive industry relies on injection molding for consistent production.
- Consumer Electronics: Items such as phone housings and computer components benefit significantly from the efficiency of injection molding.
- Medical Devices: Ensuring sterile and precise components, the medical industry utilizes injection molds to produce devices and packaging.
- Industrial Equipment: Injection molding serves the industrial sector by producing various equipment and machinery parts that withstand rigorous conditions.
Choosing the Right Injection Mold Tool Provider
The choice of injection mold tool provider can significantly impact production quality and efficiency. Here are several factors to consider when selecting a provider:
- Experience and Expertise: Look for a provider with extensive experience in the injection molding industry and a proven track record.
- Technology and Equipment: Ensure the provider utilizes advanced technology and state-of-the-art equipment to achieve optimal results.
- Customization Options: Choose a provider that offers custom tooling solutions tailored to your specific needs.
- Quality Assurance: Verify the provider's commitment to quality assurance and adherence to industry standards.
- Pricing: While cost is essential, evaluate it alongside the quality of service and products offered.
Future Trends in Injection Molding and Metal Fabrication
The landscape of injection molding and metal fabrication is ever-evolving, driven by technological advancements and changing market demands. Some emerging trends include:
1. Smart Manufacturing
The integration of IoT (Internet of Things) in manufacturing processes is leading to smarter injection molding operations, where real-time data analysis optimizes production processes.
2. Eco-Friendly Materials
As sustainability becomes a priority, manufacturers are increasingly exploring biodegradable and recyclable materials suitable for injection molding.
3. 3D Printing Innovations
The combination of injection molding and 3D printing technologies is creating new opportunities for rapid prototyping and production efficiency.
4. Automation and Robotics
Automation in injection molding processes enhances speed and precision, reducing the reliance on manual labor and human error.
Conclusion
In conclusion, the role of the injection mold tool in metal fabrication is indispensable. Its ability to produce high-quality, precise, and cost-effective parts makes it a cornerstone of modern manufacturing processes. As industries continue to evolve and innovate, the importance of injection molding will only increase, paving the way for smarter and more sustainable manufacturing solutions.
For more insights and high-quality injection mold tools, visit deepmould.net today!