Unlocking the Future of Metal Fabrication Through Prototype 3D Printing
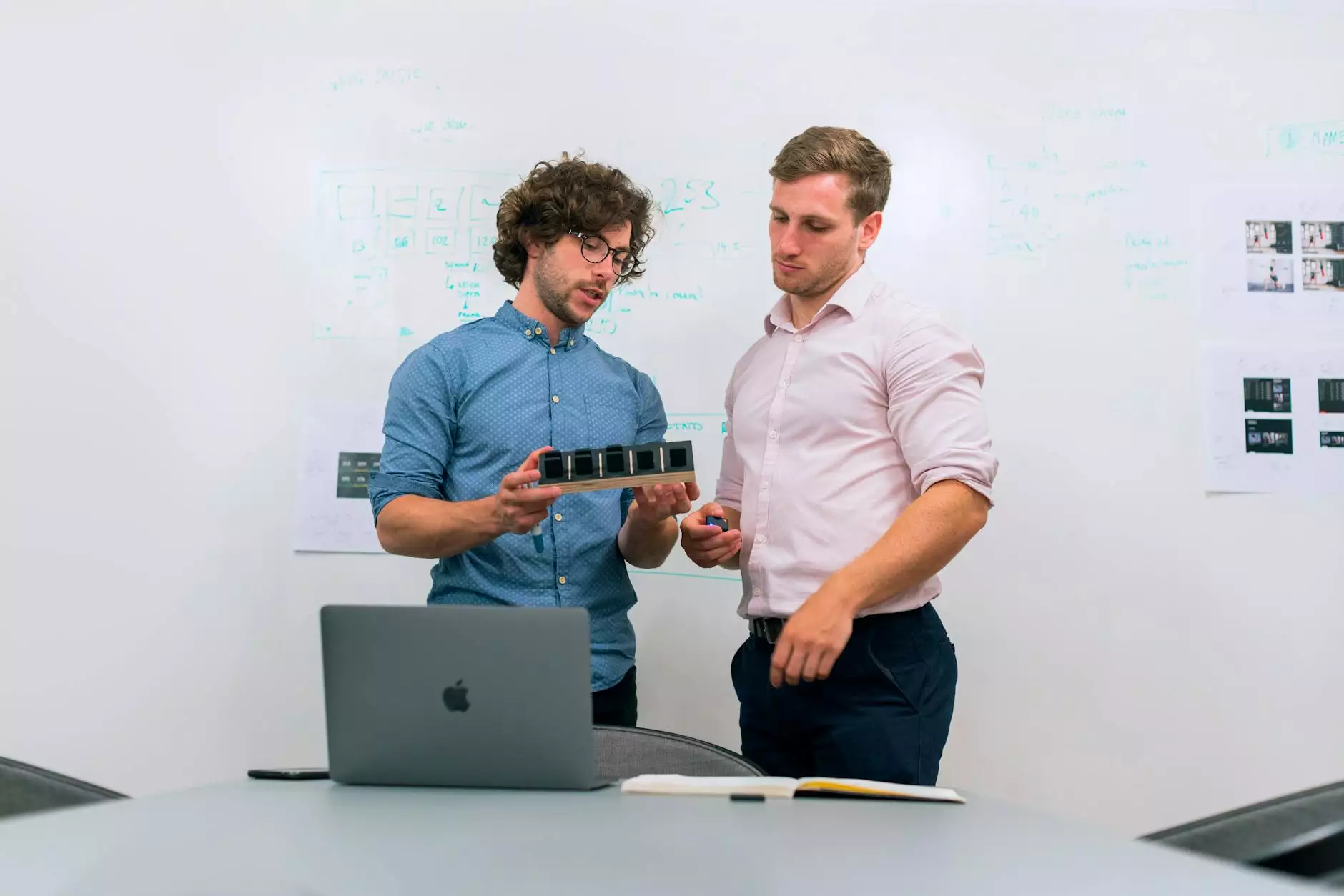
In today's fast-paced industrial landscape, innovation is the key to staying ahead. Businesses are constantly seeking ways to enhance production efficiency, reduce costs, and improve product quality. One of the most groundbreaking advancements in recent years has been the rise of prototype 3D printing, particularly within the realm of metal fabrication. This article delves into the significant impacts that prototype 3D printing has on the industry and how companies like DeepMould are leveraging this technology to revolutionize their offerings.
The Evolution of Metal Fabrication
Metal fabrication has a storied history, evolving from traditional methods involving manual labor and primitive tools to sophisticated techniques that incorporate computer-aided design (CAD) and automation. With the introduction of prototype 3D printing, a new dawn of possibilities has emerged. This technology enables the creation of intricate metal components with exceptional precision and speed.
What is Prototype 3D Printing?
Prototype 3D printing refers to the process of creating physical models from digital CAD files, allowing designers and engineers to visualize, test, and iterate their designs quickly. Unlike traditional manufacturing methods, which often require substantial setup time and costs, 3D printing offers a flexible and efficient approach to prototype creation. This technology utilizes various materials, including metals, to produce functional prototypes that can be used for testing and validation before mass production.
Benefits of Prototype 3D Printing in Metal Fabrication
The integration of prototype 3D printing in metal fabrication has ushered in numerous advantages that enhance the overall production process:
- Rapid Prototyping: Companies can produce prototypes within hours, enabling faster design iterations and reducing the time to market.
- Complex Geometries: 3D printing allows for the creation of intricate shapes and designs that would be extremely difficult or impossible to achieve through traditional fabrication methods.
- Cost Efficiency: Reduced material waste and lower production costs make prototype 3D printing a financially viable option for businesses.
- Customization: 3D printing offers unparalleled customization options, allowing businesses to tailor their products according to specific client needs.
- Material Variety: Advances in 3D printing technology have expanded the range of metals available for prototyping, including aluminum, titanium, and stainless steel.
- Ease of Modification: Designers can make adjustments to their models digitally, which can be reflected immediately in the prototype, streamlining the design process.
Applications of Prototype 3D Printing in Metal Fabrication
Many industries are harnessing the power of prototype 3D printing to enhance their production capabilities. Some notable applications include:
Aerospace Industry
The aerospace sector demands precision and performance, where even the slightest design flaw can lead to catastrophic failures. 3D printing allows engineers to create lightweight yet strong components, thus improving fuel efficiency and flight performance.
Automotive Sector
Automakers utilize prototype 3D printing to develop prototypes for parts, enabling rapid testing and validation of designs. This facilitates innovation in vehicle design while minimizing costs and production time.
Medical Devices
In the medical field, customized implants and prosthetics are becoming increasingly common. 3D printing provides the ability to produce tailored solutions that enhance patient outcomes.
Industrial Machinery
Manufacturers of industrial machines rely on rapid prototyping to test new designs and improve existing machines, ensuring they meet the evolving needs of the market.
Challenges and Future of Prototype 3D Printing
While the benefits of prototype 3D printing are undeniable, there are challenges that the industry must address:
- Material Limitations: Although the variety of metals available for 3D printing is growing, some materials still pose challenges regarding strength and durability.
- Technical Expertise: The transition to 3D printing requires skilled labor and knowledge of advanced technology, creating a need for continuous training and development.
- Regulatory Hurdles: Industries such as aerospace and medicine are heavily regulated, and ensuring that 3D printed components meet safety requirements can be complex.
Despite these challenges, the future of prototype 3D printing looks promising. Ongoing research and development are expected to yield advancements that will enhance material properties and expand the applications of this transformative technology.
DeepMould: Pioneering Prototype 3D Printing in Metal Fabrication
At DeepMould, we are at the forefront of adopting prototype 3D printing technology to elevate our metal fabrication services. Our commitment to innovation helps our clients achieve exceptional results, whether they are developing prototypes for new products or enhancing existing designs.
Our Expertise in Metal Fabrication
As a leading provider in the field, DeepMould specializes in:
- Custom Metal Fabrication: We offer tailored solutions to meet our clients’ specific requirements.
- Prototype Development: Utilizing advanced 3D printing techniques, we create functional prototypes that help our customers visualize their designs.
- Production Runs: Our streamlined processes and state-of-the-art equipment enable us to provide efficient production runs, whether short or long.
- Materials Expertise: Our team has extensive knowledge of various metals suitable for different applications, ensuring optimal results for every project.
Why Choose DeepMould?
Choosing DeepMould means opting for quality, precision, and unparalleled service. Our dedicated team of professionals is committed to delivering outstanding results that exceed expectations. By leveraging prototype 3D printing, we empower businesses to innovate and thrive in a competitive marketplace.
Conclusion
In conclusion, the integration of prototype 3D printing in metal fabrication is transforming the way industries design and produce components. With its remarkable benefits, from rapid prototyping to cost savings, businesses can unlock new levels of innovation. Companies like DeepMould are leading the charge in this field, providing the tools and expertise necessary for success. As challenges are addressed and technologies evolve, the future of prototype 3D printing looks bright, promising to redefine the standards of quality and efficiency in metal fabrication.